WE’RE A BATTERY CELL COMPONENT MANUFACTURER CREATING THE FUTURE OF MOBILITY
This comprehensive guide walks you through what you can expect with IntriPlex as your battery cell component manufacturer.
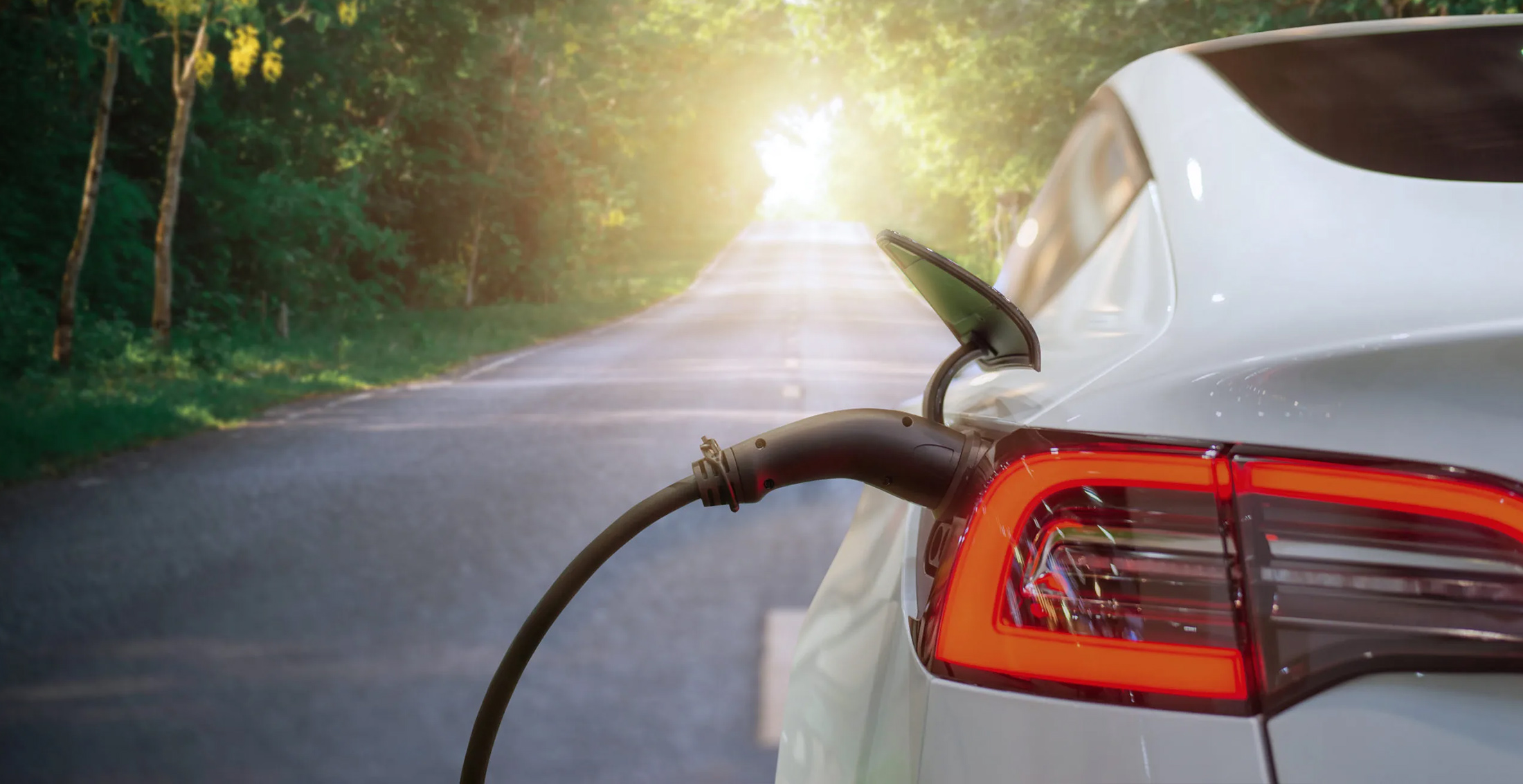
We’re at the forefront of the lithium-ion battery cell revolution precisely because we’ve been developing innovative solutions for demanding, rapidly expanding global industries for more than 35 years.
At IntriPlex, we’re not simply a battery cell component manufacturer. We go beyond mere manufacturing; we’re architects of progress, working closely with lithium-ion battery cell producers to engineer high-performance custom components and assemblies for cylindrical and prismatic cell formats. Our solution-oriented mindset, complemented by class-leading technical support, and our unrivaled ability to maintain ultra-tight tolerances over vast quantities, positions us as the optimal choice for ensuring your future success.
Wherever you produce batteries, IntriPlex can support you, providing engineering expertise and top-notch service for stamping your battery components. Be a leader in the lithium-ion battery industry with IntriPlex as your battery cell component manufacturer.
Topics we cover
How Does IntriPlex Fit into Your Supply Chain as a Battery Cell Component Manufacturer?
Why choose IntriPlex as your battery cell component manufacturer? We stamp over 800 million precision components annually, utilizing extensible technology for rapid scaling tailored to your production requirements. Partnering with us means becoming part of a trusted network of global companies relying on IntriPlex for their intricate metal component needs. We bring improvements across the entire value chain, enhancing battery performance. Let’s explore the key advantages of choosing IntriPlex as your battery cell component manufacturer.
Innovative ideas need a strategic partner
We like to think of ourselves as an extension of your team. At IntriPlex, we are your trusted battery cell component manufacturer, offering tailor-made solutions and services that fit your battery cell component manufacturing requirements seamlessly. This allows you to focus on your core business while we make sure risks are minimized, problems are solved and the execution of design, development, and production of mission-critical stamped components is completed without a hitch.
Our Innovation Center is a place where you and your team can ideate and prototype freely. Staffed with a dynamic mix of highly experienced engineers, we collaborate closely with you at every stage of your product design and development process. Collaboration is never too early; we begin by asking strategic questions and brainstorming alongside your team. Then we craft an informed plan to set your project on the right path. Our focus on precision metal stamping, coupled with extensive expertise in various scientific disciplines, provides a competitive advantage in delivering innovative solutions for your battery production.
Exceptional service
Throughout the battery cell component development process, we work side by side with our customer teams offering strategic manufacturing resources, in-house technology development, and completely integrated logistical support. We provide a broad range of services that satisfy both the requirements of our customers and the higher levels of compliance and performance expectations of today.
Efficiency with every step
Streamlining time to market while maintaining an unwavering commitment to quality is a priority in our role as the driving force behind battery cell component innovation. Our proactive approach ensures a harmonious balance between these two imperatives throughout the development process, minimizing both time and cost.
As a battery cell component manufacturer, we recognize the paramount importance of expediting time to market while upholding unwavering commitment to quality. Our proactive approach ensures a harmonious balance between these two imperatives throughout the development process, minimizing both time and cost.
Quality controls are seamlessly integrated into every project phase, virtually eliminating issues and surprises. To further expedite processes and enhance accuracy, we design our tooling in-house, simulating it before construction. This approach condenses what might typically take 5-7 tooling iterations into 2-3.
When it comes to our presses, we exclusively utilize Bruderer presses renowned for their unparalleled precision and reliability. Our presses run from 100 to 1,100 strokes per minute depending on the part geometry and requirements.
Global presence for increased agility & decreased costs
As a US-based battery cell component manufacturer, we are thrilled to contribute to the momentum positioning U.S. manufacturing as a leader in the battery industry. IntriPlex operates manufacturing facilities in North America and Southeast Asia, offering you the flexibility to avoid overseas production costs such as transit, inventory, warehousing, and logistics.
Choosing IntriPlex means your battery components can be economically produced nearby, eliminating the need for extensive overseas expenses. In comparison to companies exclusively manufacturing overseas, we offer a shorter lead time for development. Experience real-time support communication and increased operational efficiency as your products have less distance to travel.
Superior technology & unmatched capabilities equals better products
Partnering with us as your battery cell component manufacturer means we will join you in the rigorous pursuit of developing technologies and products that propel your battery production forward.
IntriPlex offers significant benefits to your battery development process in four key ways.
First, we can fulfill all of your current precision stamping needs for battery cell components. You can count on a seamless transition in shifting your current stamped part production to our facilities.
Secondly, our design and engineering services offer transparency, flexibility, collaboration, and proactive engagement. Work with us at our Innovation Center, granting hands-on access to labs, testing, advanced analysis tools, materials, and a dynamic design and engineering team. This collaborative approach is a primary reason why customers repeatedly choose IntriPlex.
Thirdly, our U.S.-based customers gain a distinct competitive advantage through a singular U.S. supply source.
And finally, IntriPlex excels in improving upon battery components sourced from other suppliers, regardless of their production methods. Our precision metal stamping technology is unrivaled, enabling the creation of unique geometries that were previously unattainable using traditional stamping methods. At IntriPlex, we are dedicated to advancing battery cell component manufacturing for superior outcomes.
Which Battery Cell Components Can IntriPlex Produce with Precision Forming?
IntriPlex takes pride in the quality, innovative capabilities, flexibility, and efficiency of our battery component design, development, and production. We don’t believe in a one size fits all approach. We design, develop, and customize battery cell components to your specifications and end-application requirements.
BATTERY COMPONENTS WE MAKE
Anode and Cathode Collectors
Busbars and Brackets
Burst Discs and Diaphragms
Contacts and CIDs
Poles & Covers
Retaining Rings
Sealing Caps
Vents
Curious if we can stamp a product not listed here? Let’s discuss! We are always scouting out new opportunities to broaden our battery cell component portfolio.
IntriPlex metal stamping technology is versatile and constantly evolving, and our R&D department is developing new “stampable” components all the time. We’re a battery cell component manufacturer you can count on for your custom battery cell component needs.
What Are Our Battery Lid Assembly Capabilities?
IntriPlex is equipped with advanced manufacturing technology that facilitates the complete assembly of battery lids and support our customers’ battery production process. Our specialized material handling, assembly, and final product testing capabilities ensure the creation of safe, compact, and powerful battery lids.
As a leading battery cell component manufacturer, every facet of our operations contributes to the development of a more robust, superior, and reliable battery, ultimately saving our customers time and providing them with peace of mind.
INTRIPLEX SERVICES FOR BATTERY LID ASSEMBLY
Specialized high-volume, precision automation
Laser and resistance welding
Plating and hardening
World-class cleaning processes
Gluing and coating
Tight tolerance & high consistency
Full lid assembly
How Will IntriPlex Keep Customers’ Costs Down?
We understand that the stakes are high when you’re mass-producing precision-stamped parts. No doubt you want a battery cell component manufacturer who will keep costs down without sacrificing quality to ensure you get the best price for your stamped battery cell components.
At IntriPlex, we believe there are no shortcuts to success, and we’re willing to go the distance to make sure we do things the right way. Everything we do is built on the cornerstones of precision-level quality and customer satisfaction.
Here are four ways we help our customers get the best value for their investment:
Stamping the “unstampable”
Stamping is one of the most economical methods of manufacturing, however, the issue has been that not all products are “stampable.” We change this by developing ways of stamping components never stamped before, enabling you to reduce your costs, increase your revenue, and grow your business.
Negotiated pricing on raw materials
We’ve scoured the globe for the very best and purest raw materials. We’ve also built strong relationships with our raw material vendors to ensure a steady supply of premium raw materials at excellent contract prices. This means you will get the necessary material performance and also the best value.
Complimentary research & development services
At IntriPlex, our commitment to meeting customer needs is paramount. We believe that our development efforts are at the core of our strategic advantage and so all of our R&D is in-house, and we don’t charge for basic development tasks. Our customer’s success is our success and our mission is to promote a win-win experience.
A focus on high-volume manufacturing
Many metal stamping companies will tell you they will do any size run you need, from small to large. We work exclusively with customers who have large-scale manufacturing requirements. While this means we aren’t able to take on every project request we get, we ensure that the cost savings that are built from producing more parts faster reduces the overall cost of production per unit and inevitably make the ROI more economically attractive for our customers.
More importantly, we guarantee pricing transparency, assuring our customers that prices are not inflated to compensate for losses incurred by serving low-volume production needs.
Working with a metal stamping partner who has mastered the art of customization and possesses the flexibility to adapt to your unique requirements is essential for a successful project. It’s not just about meeting your expectations; it’s about exceeding them with tailor-made excellence. When seeking a metal stamping company, keep this in mind as it can make a world of difference in the outcome of your project.
How Will IntriPlex Components Benefit Your Design Engineer?
The need for high-quality battery manufacturing services to meet the demand for high-quality batteries is rising in record time. We understand the importance of selecting the right battery cell component manufacturer is critical, that’s why we help your design engineer overcome all their challenges and answer their most pressing questions so that together, we will launch better batteries. Here’s how:
Eminent accuracy
Engineers demand precision, and at IntriPlex, we deliver exactly that. We employ some of the strictest controls on geometries and specifications in the industry. We design and build to exacting standards, giving your engineers the confidence that their designs will work with absolute consistency. Our typical tolerances include precise measurements across various dimensions.
OUR TYPICAL TOLERANCES
Ultra-thin micro metal part capability
Our process generates small parts with extreme fidelity, and we deftly handle part specifications with the most impressive tolerances and exacting standards. As battery cells for the EV/HEV and Energy Storage markets shrink, more and more of their components will fall under our purview. That means the value we can bring your engineering team will scale as the technology matures.
Others see impossible, while we find a way
IntriPlex’s ability to stamp parts that no other manufacturer can manage is a major boon to your engineers, allowing them to think further outside of the box than previously possible. We empower your engineers to, visualize, dig in, and execute. Our innovation portfolio spans diverse markets including data storage, telecommunications, medical, and automotive.
Does IntriPlex Have the Capacity to Grow in Parallel with Our Increasing Battery Component Needs?
What’s needed today is flexible battery cell component manufacturing for new formats and technologies. As the demand for battery energy storage continues to grow, you’ll need a partner that can keep pace with your growing production demands. And as a high-volume manufacturer, producing close to 1 billion parts a year, we assure you that our process is extremely scalable and transferable.
Versatile manufacturing
All of our customers have high-volume needs so we are accustomed to increasing our stamping capacity when needed. Once we have built the necessary tooling, production can be scaled quickly and easily. Additionally, multiple jobs can be interchanged quickly with a single press allowing for scheduling flexibility.
What Types of Materials Can IntriPlex Work With?
The push for lightweight vehicles, driven by environmental policies and customer preferences, has become synonymous with efficiency, performance, emissions reductions, and cost savings, especially in the context of extending EV range. This demand challenges metal stamping companies to engage with material thicknesses they are unfamiliar with.
However, at IntriPlex we have the know-how to produce parts from materials as thin as 0.00049”, and we regularly precision form micro-miniature parts, packing thousands of pieces in the palm of your hand.
We work with a diverse range of exceptionally pure and high-performing materials, including special metals. If you have a project with unique material requirements, we welcome the opportunity to review your specifications.
MATERIALS WE COMMONLY WORK WITH
Aluminum
Copper
Stainless steel
Brass
Carbon steel
Clad and inlaid
Precious metal plated material (including selective plating)
What Are IntriPlex’s Lead Times?
We know that one of your biggest questions is “When can I get it?” We understand that to meet the upsurge in electromobility, battery cell component manufacturers need to offer increased speed and efficiency. Lead times will vary depending on the project, but compared to other stamping companies our lead times are very competitive.
Efficiency through project management
Our multidisciplinary environment promotes collaboration among our product managers and technical teams while capturing your needs and meeting compliance requirements. This systematic approach with a focus on cross-functional teamwork provides company-wide transparency throughout every step to eliminate delays and promote a smooth and efficient workflow.
A practical, proactive approach
Additionally, we frequently employ “insertable” tooling to initiate running prototypes that faithfully represent the final mass-produced products. This strategy allows us to progress with the development process while custom tooling is being brought online. Once the full production line is operational, our capacity becomes massive and scalable. Need to double the number of parts from your last order? No problem. Our flexibility enables us to precisely match production to your evolving needs.
How Does IntriPlex Support Its Customers?
Thanks to our global presence and heterogeneous team IntriPlex offers customers a partnership ecosystem for the development of battery cell components. Making innovation happen takes a collaborative, human-centered approach from the start, so we invest side-by-side with our customer teams. Our goal is to deliver an unparalleled experience as your battery cell component manufacturer.
Expertise dedicated to you
We take customer service very seriously, so we place local customer service professionals in every country we do business. All of our customer service professionals are degreed engineers. You will have access to highly-trained personnel familiar with your project. No matter how technical your questions are, you will always get the answers you need, quickly and accurately.
Component design & analysis
Whether performing a detailed analysis to determine the suitability of a certain design geometry or sitting with our customers to discuss conceptually their particular requirements for a new component, our commitment to getting them what they need is paramount. Our robust and comprehensive design analysis predicts the physical behavior of the part which ensures more predictable and reliable prototyping and testing.
Design for manufacturing
We will challenge the design at all levels to ensure it is optimized in every way for performance, quality, and manufacturing without any unnecessary costs embedded into it. Our exhaustive design for manufacturing investigation reduces redesign work and cost, improves product quality, and speeds up your time to market.
Design for cost
We employ a systematic approach to controlling the costs of product development and manufacturing so that we provide value to all links of the manufacturing chain. We pay special attention to your target costing and all manners of project scope, staffing, scheduling, and coordination so that your final product is executed within your costing parameters. We look for opportunities to optimize product design for cost efficiency, and we manufacture using the most efficient processes.
Prototyping
We offer a systematic and collaborative approach to transform conceptual designs into tangible prototypes. During this crucial phase, we engage closely with our customer, conducting thorough design analysis, predicting physical behaviors of the parts, and ensuring optimal performance, quality, and manufacturability. Prototyping allows customers to visualize and test the components in real-world applications, enabling iterative refinement and minimizing the risk of costly errors during the later stages of production.
Testing & measurement
At IntriPlex, we go beyond mere print specifications in our commitment to ensuring success for our customers. Employing advanced metrology, rigorous testing protocols, and state-of-the-art tools, we aim to enhance downstream product performance. Our fully-equipped labs allow us to assemble and test products just as our customers would, ensuring a comprehensive understanding of how our parts function within the intended application.
High-volume manufacturing
Once we have ensured we have the perfect specification adherence to meet your needs, we are capable of rapidly manufacturing your product and delivering it on time. Our highly automated progressive precision forming process is best suited for high-volume manufacturing.
What Support Is Provided Once a Part Goes into Production?
Over the years, IntriPlex has built a reputation for excellent customer service – which is why customers come to us repeatedly. You will enjoy the same high level of support you get during battery cell component development as you will after your parts transition into production. We ensure your needs are met well beyond the time the product goes to market. IntriPlex post-production services enable our customers to minimize inventory exposure, eliminate multiple administrative costs, and increase response time to their customers.
An end-to-end product development team
Upon partnering with us, you’ll be assigned a team of product and quality engineers that will monitor production and work with you throughout your relationship with us. Did your requirements change? IntriPlex can build and test prototypes or evaluate new critical to-function parameter requirements until a solution is found. We aim to resolve issues efficiently and professionally while working closely with our development team, and communicating up-to-date developments.
Quality control
All of our products and services go through a comprehensive quality management system, in compliance with ISO 9001:2015. This means that we go further than checking the quality of the products, we also address problems that may arise after production but before shipment. We offer custom, specialty packaging to make sure your parts remain organized and in pristine condition, and we aim to seek and address any problem that might arise before your order arrives at your door.
Logistical support
We will work with you to find the best way to get your products to you which is in line with your budget and objectives. Should you need your products shipped overseas, we will iron out the fine details when it comes to customs and having the required documentation that is needed.
What Is the IntriPlex Quality Management System?
Our IntriPlex Quality Management System is designed to ensure our customers receive the highest level of quality possible. When we say “precision,” we mean it. We do extensive and ongoing testing using state-of-the-art equipment to guarantee the strictest tolerances. Our quality department leverages state-of-the-art technology, including:
TECHNOLOGY WE COMMONLY USE
Laser interferometers for geometry shape control
CNC Visual Measurement Systems for dimensional control
30x Stereo microscopes for visual inspection
Custom mechanical gauges with resolutions down to 25 nanometers
Class 10K clean rooms for product inspection
Component cleanliness measurement and control down to 0.2-micron particles
Scanning Electron Microscopes with EDS for components and raw material evaluations
All of our processes are monitored and documented for incremental improvement and maximum control. The InfinityQS quality control software system comprehensively tracks all our activities across the entire production line. Our commitment to transparency includes assigning unique lot numbers to each batch of produced parts, facilitating the tracking of critical production details, including the raw materials used.
Why Should You Trust IntriPlex Precision Forming for Your EV Battery Cell Components?
IntriPlex was created with a focus on people, innovation, and evolution without borders, growing solidly, and globally over the years. In a dynamic and constantly changing world, we are guided by our vision of continually pioneering and creating prosperous relationships marked by the exchange of ideas and experiences. We are much more than a metal stamping company or a battery cell component manufacturer, our passion for the will to make a difference guides our constant advancement and evolution.
IntriPlex is committed to the highest professional standards for the protection of our customers’ confidential information. We have strict measures in place to safeguard the security of your information, including non-disclosure agreements with all our customers to ensure confidentiality and mutual understanding regarding intellectual property. Our personal assurance and our track record are a reflection of our professionalism and integrity.
Transparent & collaborative
We know that developing a new stamped product can be a complex undertaking. In addition to our wide-ranging expertise and overview of every aspect of the process, we are committed to one another as team players first and foremost.
Our culture encourages honesty and respect, while always challenging ourselves and each other. We believe in models of partnership optimization. That’s why all our communications and processes are built on clarity, transparency, and accountability. We’re all about cutting distances – in work, in relationships, and in technology so we invest everything to create long-lasting mutually rewarding experiences with our customers.
A commitment to excellence
We believe only the highest level of service and commitment can yield exceptional results for both our customers and our team. Our knowledge and expertise in various scientific disciplines provide a competitive advantage in designing and delivering innovative solutions to our customers.
OUR AREAS OF EXPERTISE
Mechanical Engineering
Electrical Engineering
Chemical Engineering
Materials Engineering
Manufacturing Technology
Signal Processing
Contamination Control
Lubricants and Tribology
Magnetics
Fluid Hydrodynamics
Particle Dynamics
Design G&T
Always agile, always advancing
At IntriPlex we are always striving to outperform yesterday. Combining creativity and innovation to invent unique technology, we’re a team that continually delivers new solutions that are as ground-breaking as they are practical.
We never forget that it can take considerable time and effort to develop a product. That’s why we respond to changes as they arise, taking opportunities when they present themselves to achieve the best possible results. Our flexible approach means that we adapt rapidly, without compromising on quality.
We think beyond and lead where others follow
We are curious about the future and so we always look further. We lead a streamlined, effective process, backed by 35+ years of continual and diligent research, engineering know-how, innovative technology, and agile procedures.
We consistently deliver world-class products and services – reinventing the metal stamping industry with advanced technology, thinking big, and acting bigger. In each industry we participate in, we’ve brought solutions to stamp previously impossible geometries allowing for significant cost savings, higher quality, and more repeatable components – and we’ve paved the way for others to follow.
Together for Your Success in Battery Component Manufacturing
Selecting a metal stamping company is not merely a transaction; it’s the forging of a partnership based on trust, expertise, and shared goals. When you embark on this journey, consider not just the tangible attributes, but also the invisible threads that create a bond of confidence.
IntriPlex enables a more efficient, innovative, and reliable experience in battery cell component manufacturing. We work with you from design to production and ensure the entire value chain in battery component production is executed seamlessly. Partnering with a trusted battery cell component manufacturer that has first-hand experience in all critical domains of the battery industry like engineering, and manufacturing and will help you level up in a rapidly evolving battery technology landscape. We look forward to supporting you as your battery cell component manufacturer.