Crafting Precision: The World of Metal Stamping Parts
In the complex landscape of modern manufacturing, there exists a hidden hero, often overlooked yet indispensable in countless industries: metal stamping parts. These unassuming metal components born of precision and purpose wield immense influence behind the scenes of products we encounter daily, from the car you drive to the smartphone you hold.
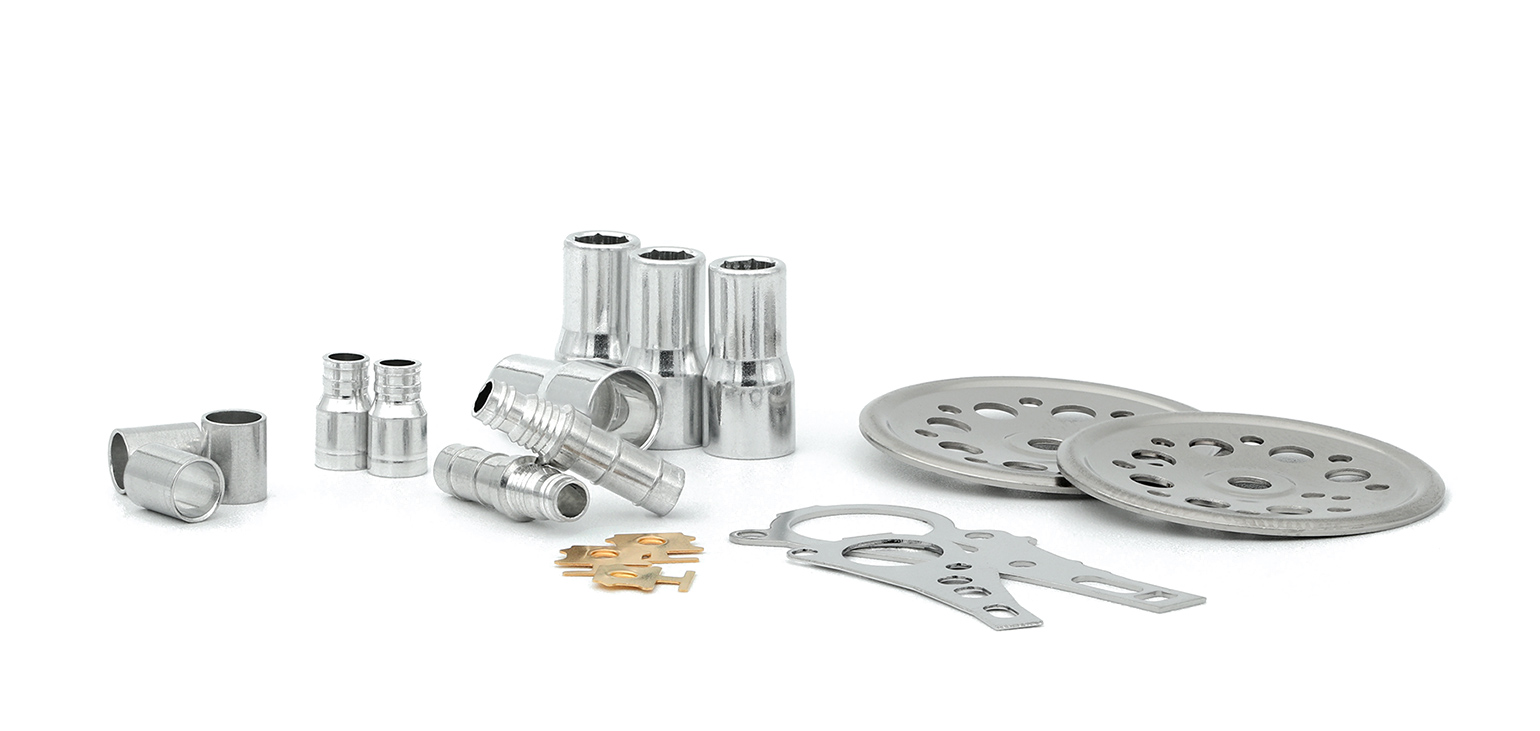
Topics we cover
Understanding Metal Stamping Parts
Metal stamping parts are the carefully crafted outcomes of a specialized manufacturing process known as “metal stamping.” These components, found in various forms and functions, serve diverse purposes, from intricate connectors for the telecommunications industry to essential elements in the batteries that power electric vehicles.
While they may appear as simple pieces of metal at first glance, these parts are integral to our technological landscape. The seamless operation of our vehicles, the safety of our flights, and the functionality of our electronic devices all hinge on the precision and reliability of these components. They represent meticulous engineering, resulting from a delicate interplay between raw materials, precision tools, and intense pressure. The advancement of industries frequently depends on the continuous adaptation of the metal stamping industry and the innovation of metal stamping technology. Metal stamping parts are the silent enablers of progress.
“Metal stamping parts are the silent enablers of progress.”
The Metal Stamping Process
Metal stamping is essentially a coordinated dance between machinery and material. It is a manufacturing technique that transforms flat metal sheets or metal strips into finely detailed, three-dimensional components. The process requires not just the right materials, but also the expertise of engineers and the power of specialized machinery. A meticulously choreographed sequence of stations within the die forms, cuts, and pierces the metal inside the press. What emerges is a precisely crafted metal stamping part – an embodiment of design and engineering finesse.
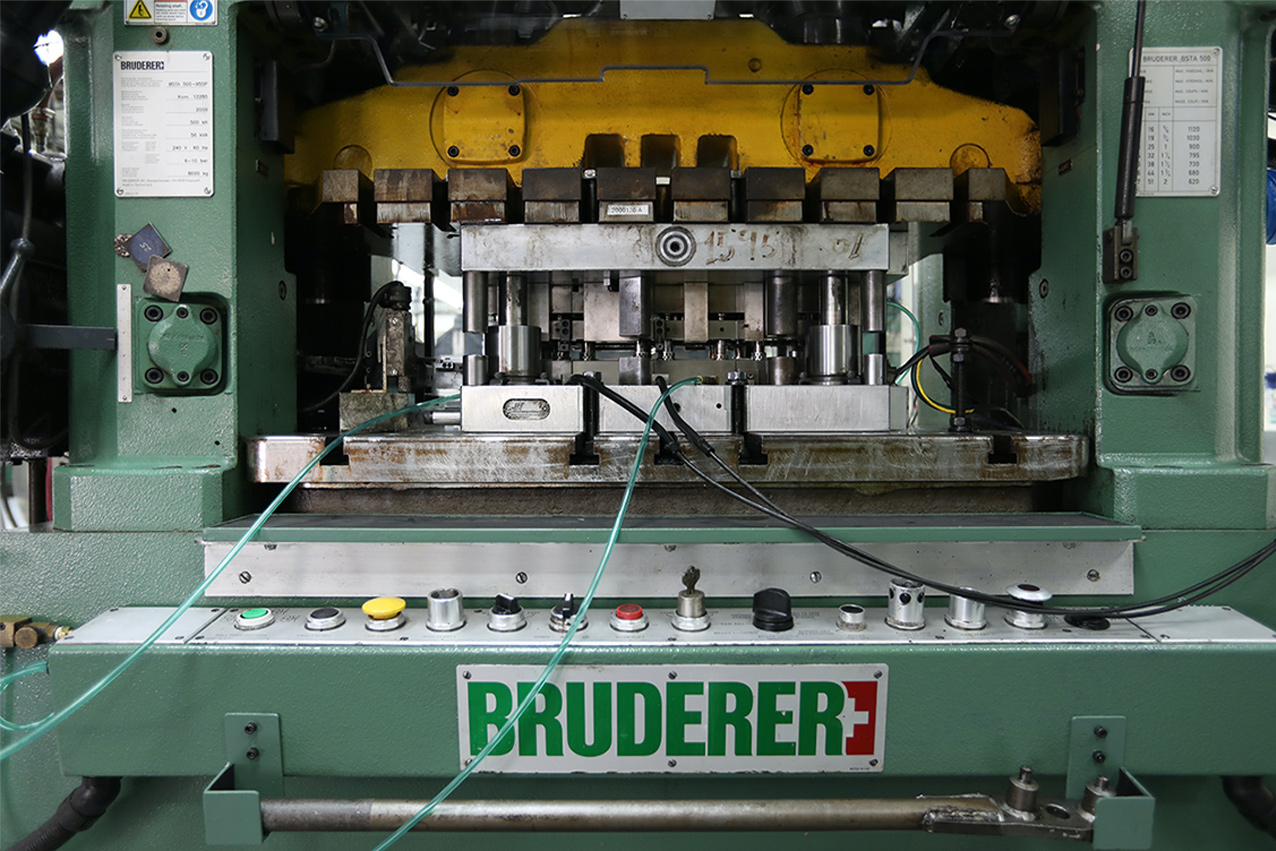
Materials at the Core
The metal stamping process thrives on the versatility and inherent properties of certain metals, each carefully selected to suit the intended purpose. Steel, aluminum, and copper are the most commonly chosen options. These materials have qualities that are distinctive and well-suited to various applications.
Steel: Known for its strength and durability, steel is a stalwart choice in metal stamping. It’s the go-to material when structural integrity and longevity are paramount. The ability to withstand harsh conditions and heavy use makes steel an ideal candidate for metal stamping parts used in demanding environments.
Aluminum: In contrast to the sheer might of steel, aluminum brings a lightweight versatility that is essential for certain applications. Its corrosion resistance and excellent thermal conductivity make it a preferred choice for parts in the automotive, aerospace, and electronics industries.
Copper: Copper’s exceptional electrical conductivity makes it the material of choice for electrical connectors and components. Its ability to efficiently transmit electricity without significant loss in performance is a crucial characteristic in numerous electronic devices.
Key Considerations in Material Selection
While the selection of materials may appear straightforward, it involves careful consideration of key factors.
1. Application Requirements: The foremost consideration is the specific needs of the application. The material must align with the demands of the environment, whether it involves exposure to extreme temperatures, corrosive elements, or high mechanical stress.
2. Material Properties: Understanding the inherent properties of each metal is essential. For instance, the strength, ductility, and electrical conductivity of steel, aluminum, and copper are distinct and must align with the intended function of the metal stamping part.
3. Cost and Availability: Practical considerations often play a role. The cost of the material, as well as its availability, can influence the choice, particularly for high-volume manufacturing.
4. Manufacturability: The chosen material must be compatible with the metal stamping process. Some metals are more challenging to work with due to their ductility or hardness, and this must be factored into the selection.
5. Endurance and Reliability: Whether a part is intended for the automotive industry, electronics, or any other application, its endurance and reliability are paramount. The material should withstand wear and tear, ensuring a long service life for the finished product.
In the world of metal stamping parts, selecting the right material is a deliberate choice influenced by considerations of functionality, durability, and performance. This decision mirrors the precision seen in the metal stamping process, reflecting the careful judgment of engineers and manufacturers.
Design Considerations for Metal Stamping Parts
For engineers and designers, delving into the world of metal stamping parts entails a deep understanding of not just the manufacturing process itself, but also the intricacies of crafting a design that can be seamlessly translated into a functional component. The following section explores the key design considerations that are essential for creating parts optimized for metal stamping.
Material Compatibility
Before diving into the intricate details of design, it’s crucial to ensure that the chosen material aligns with the proposed design. Certain materials may be more suitable for complex shapes or specific functions. For example, while steel is renowned for its strength, aluminum, and copper offer more malleability for parts that require intricate geometries.
Tolerance and Precision
One of the defining characteristics of metal stamping is the high level of precision it offers. Designing with tight tolerances in mind ensures that the finished metal stamping part aligns perfectly with the intended specifications. Engineers must take into account the tolerances achievable in the stamping process and design components that stay within these limits.
Design for Manufacturability
A well-designed part should be as easy to manufacture as it is functional. This means considering the manufacturability of the part during the design phase. For example, sharp corners, complex undercuts, or overly intricate shapes can make the manufacturing process more challenging. Designers should aim for simplicity wherever possible.
Consideration for Material Thickness
The thickness of the material has a direct impact on the feasibility and cost of the metal stamping process. Designing with the thickness in mind is essential. Typically, thinner strips or sheets of metal are easier to work with and are more cost-effective. However, the choice of thickness should align with the intended function and strength requirements of the part.
Material Waste Reduction
Efficiency is a key principle in metal stamping. Minimizing material waste is not only environmentally responsible but also economically beneficial. A good design should optimize the use of the material, reducing scrap and costs.
Radii and Fillets
Sharp corners or edges can lead to stress concentration points, which may compromise the durability and structural integrity of the part. Incorporating radii and fillets into the design distributes stress more evenly and can prevent premature failure.
Avoiding Wrinkles and Cracks
Design your part to avoid potential issues like wrinkles, cracks, or tearing during the stamping process. Minimize internal angles, as sharp corners can lead to material deformation. Curved transitions and filleted edges help prevent these problems.
Draw Ratios and Wall Thickness
Understanding draw ratios – the relationship between the material’s initial thickness and its final shape – is key. High draw ratios can lead to material thinning, while low draw ratios can result in wrinkles or tearing. Be mindful of the initial wall thickness and how it may change during the stamping process.
Success in designing metal stamping parts requires a marriage of creativity, engineering acumen, and a deep understanding of the process itself. Need help in designing your metal stamping parts? We can help!
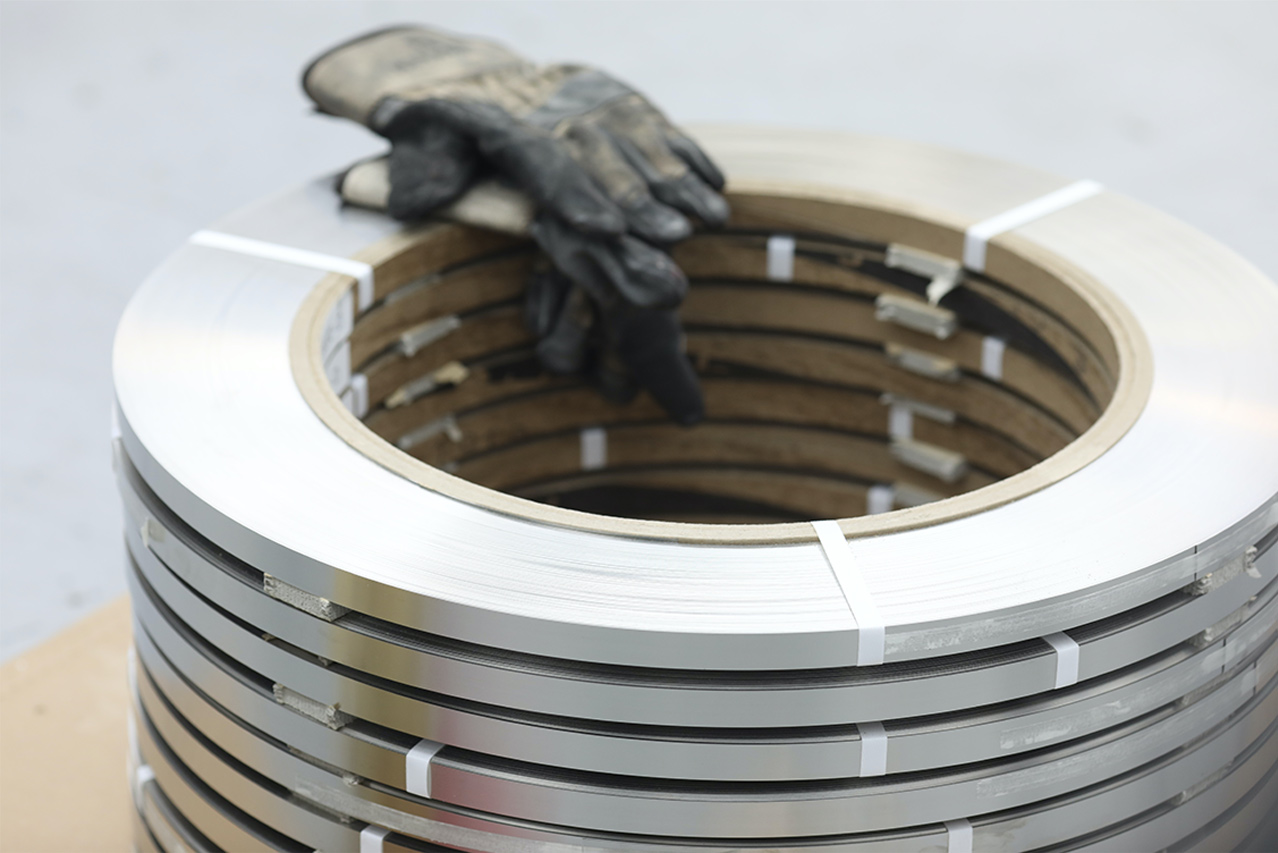
Factors Affecting the Quality of Metal Stamping Parts
The components that emerge from the metal stamping process are the result of a meticulous journey through design, tooling, precision control, and finishing touches. We’ve listed below the critical factors that influence the quality of metal stamping parts and the careful considerations that underpin their creation:
Importance of Design and Tooling
The design phase is the point of origin for a metal stamping part’s quality. It’s here that every dimension, contour, and feature is meticulously defined. The engineer’s craft involves not just conceptualizing the part but ensuring that the design aligns seamlessly with the capabilities of the metal stamping process. Every detail, from material selection to geometric complexity, must be taken into account to avoid potential issues during manufacturing.
Tooling, the heart of the metal stamping process, is the bridge between your design and the final product. The quality of tooling is paramount – a flaw in the die can propagate defects in every part produced. Engineers work in close collaboration with tool and die makers to ensure that dies are precision-engineered, guaranteeing that each stamped part is manufactured accurately.
Tolerances and Precision
Tolerances in metal stamping are exceptionally tight, often measured in micrometers. Each part must conform precisely to the design specifications to ensure its functionality and compatibility with other components. Straying even slightly from these tolerances can lead to parts that do not fit together correctly or perform as intended.
Maintaining these tolerances requires rigorous precision control throughout the stamping process. Tooling, press machinery, and quality control measures must work in concert to ensure each part is faithful to the design. Engineers often employ advanced metrology tools to verify the dimensions and geometric features of the stamped parts.
Surface Finish and Coating Options
Surface finish isn’t merely a matter of aesthetics; it’s also about functionality. For certain applications, such as in the automotive industry, a smooth surface can reduce friction and wear. In contrast, consumer electronics might benefit from a textured surface for grip. Engineers must consider these factors and select the appropriate finish to enhance the performance of the final part.
In environments prone to corrosion or wear, protective coatings become a crucial consideration. Options such as plating, powder coating, or anodizing can enhance the durability of metal stamping parts, extending their service life and reliability.
Quality Assurance and Testing
Quality assurance is the backbone of producing high-quality metal stamping parts. Each part undergoes rigorous inspection to verify that it meets industry standards and the specific requirements of the project. Visual inspections, measurements, and tests for features like tensile strength or electrical conductivity ensure that the parts are free from defects.
Ensuring that each part functions as intended is a non-negotiable requirement. In addition to dimensional inspections, parts may undergo functional testing to confirm their reliability and performance under real-world conditions.
In the intricate world of metal stamping parts, the pursuit of quality is a relentless endeavor. It requires engineers to meld their creativity with precision, demanding meticulous attention to detail at every stage of the process. In the final analysis, the quality of a metal stamping part is not just a testament to engineering prowess but a reflection of the meticulous planning and precision control that underpin its creation.
Advantages of Metal Stamping Parts
In the realm of precision engineering, metal stamping parts stand as a testament to meticulous craftsmanship and engineering excellence. Their advantages, which span from cost-efficiency to impeccable precision, are reasons why this manufacturing method is at the forefront of modern industries. As engineers, understanding these advantages and how they compare to alternative manufacturing methods is pivotal in crafting precision.
Cost-Effectiveness
When it comes to producing metal parts with efficiency and economy, metal stamping shines. Its cost-effectiveness arises from several factors.
First, the process is highly automated, reducing labor costs. Second, it generates minimal material waste, making it environmentally responsible and cost-efficient. The use of continuous coils of metal sheets or metal strips further contributes to lower material costs.
In comparison to alternative manufacturing methods such as CNC machining or die casting, metal stamping often emerges as the more budget-friendly choice for high-volume production. The ability to rapidly produce parts while minimizing material waste ensures that your investment in metal stamping delivers substantial cost savings.
High Precision and Accuracy
Precision is the very essence of metal stamping. The process achieves tolerances measured in micrometers, ensuring that each part is a replica of the design. This precision is essential, particularly in applications where components must fit together seamlessly or adhere to strict performance standards. The advantages of high precision extend beyond the aesthetic and functional quality of the parts. Precision in metal stamping often reduces the need for additional post-processing or rework, saving time and cost. In contrast, alternative methods may require more extensive finishing work to achieve comparable precision.
Scalability
Metal stamping’s inherent scalability is another compelling advantage. Whether your project requires hundreds, thousands, or millions of parts, the process can readily adapt to your needs. It thrives on high-speed production, making it an ideal choice for mass-production scenarios.
In contrast, some alternative manufacturing methods may face challenges in achieving the same level of scalability. For instance, CNC machining, while highly precise, may not match the efficiency of metal stamping for large production runs.
Metal Stamping Compared to Alternative Manufacturing Methods
To truly appreciate the advantages of metal stamping, it’s essential to consider it in contrast to alternative manufacturing methods.
1. CNC Machining: CNC machining offers superb precision but is often more labor-intensive and time-consuming, resulting in
higher production costs, especially for large volumes.
2. Die Casting: Die casting provides excellent precision and can be suitable for high-volume production, but the tooling costs are typically higher than those in metal stamping, making it a less cost-effective option for smaller runs.
3. Plastic Injection Molding: While suited for certain applications, plastic injection molding doesn’t offer the same strength and durability as metal stamping. It may also face limitations in terms of material selection and environmental resistance.
In essence, metal stamping strikes a balance between cost-efficiency, precision, and scalability that is often difficult to match with alternative manufacturing methods. It offers the best of both worlds: economy and excellence. As industries continue to push the boundaries of what’s possible, the advantages of metal stamping parts make it an indispensable player in the world of precision engineering.
“In essence, metal stamping strikes a balance between cost-efficiency, precision, and scalability that is often difficult to match with alternative manufacturing methods.”
A Precision Path to Manufacturing Excellence
In the ever-evolving landscape of modern manufacturing, where precision and efficiency are paramount, metal stamping parts emerge as a symbol of engineering finesse. The significance of these meticulously crafted components cannot be overstated; they are the unseen forces behind the smooth operation of countless industries, from automotive to electronics, and aerospace to consumer goods.
The journey from design to the final product, wrought through the metal stamping process, embodies the epitome of precision and efficiency. The advantages it offers, from cost-effectiveness to high precision and scalability, make it an indispensable choice for those who demand both excellence and economy in their manufacturing endeavors.
But here’s the crux: The path to crafting precision through metal stamping is not a solo endeavor. It’s a collaborative effort between engineers, designers, and the right manufacturing partner. The selection of the right partner is a critical factor that can elevate the quality of metal stamping parts.
Experience, expertise, and a proven track record are non-negotiable attributes that should define your choice. The synergy between your vision and their manufacturing acumen is what yields excellence. If you’re curious if IntriPlex can help design and manufacture your metal stamping parts, we’d love to hear from you.